Hoe word hoë-presisie-onderdele gemasjineer
2023-09-22
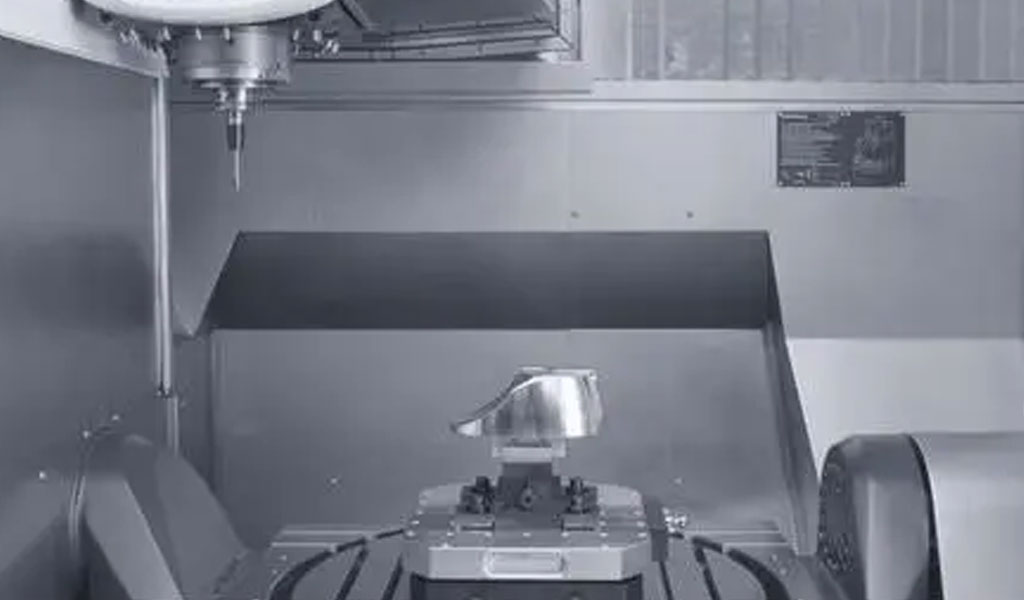
Verstaan presisiebewerking
Presisiebewerking is 'n hoeksteen van moderne vervaardiging, verantwoordelik vir die vervaardiging van ingewikkelde en akkurate komponente wat in 'n wye reeks nywerhede gebruik word. Om die betekenis daarvan ten volle te begryp, kom ons ondersoek die kernkonsepte van presisiebewerking, die belangrike rol daarvan in verskeie sektore en die historiese reis wat gelei het tot sy huidige stand van uitnemendheid.A. Wat is presisiebewerking?
Presisiebewerking verwys na 'n stel vervaardigingsprosesse wat materiaal van 'n werkstuk verwyder met 'n hoë mate van akkuraatheid en beheer, wat lei tot fyn vervaardigde komponente met streng toleransies. Hierdie proses transformeer grondstowwe, soos metale, plastiek of keramiek, in presiese dele wat aan streng spesifikasies voldoen. Die sleutelkenmerke van presisiebewerking sluit in:- Akkuraatheid: Presisiebewerking verseker dat die finale produk presies aan die beoogde ontwerp voldoen, met minimale afwyking.
- Streng toleransies: Dit maak voorsiening vir die vervaardiging van onderdele met uiters stywe toleransies, wat beteken dat die voltooide komponente nou aan gespesifiseerde afmetings voldoen.
- Uitstekende oppervlakafwerking: Presisiebewerking verskaf uitsonderlike oppervlakafwerkings, wat dikwels die behoefte aan bykomende afwerkingsprosesse uitskakel.
- Komplekse geometrieë: Dit kan ingewikkelde vorms, kontoere en kenmerke skep, wat dit onontbeerlik maak in die vervaardiging van komponente met komplekse ontwerpe.
- Herhaal: Presisie bewerkingsproseses is hoogs herhaalbaar, wat konsekwente kwaliteit oor verskeie dele verseker.
- veelsydigheid: Dit kan op 'n wye reeks materiale toegepas word, wat dit geskik maak vir diverse industrieë.
B. Belangrikheid van presisiebewerking
Presisie bewerking het 'n geweldige betekenis in verskeie kritieke industrieë, wat verskeie aspekte van ons daaglikse lewens beïnvloed. Hier is 'n paar dwingende redes vir die belangrikheid daarvan:- Lug- en ruimtevaartbedryf: In die lugvaartsektor is presisiebewerking onontbeerlik vir die vervaardiging van komponente wat uiterste toestande weerstaan. Vliegtuigenjins, landing rat, en strukturele elemente maak staat op presisie-gemasjineerde onderdele vir veiligheid en werkverrigting.
- Mediese toerusting: Mediese toestelle soos chirurgiese instrumente, prostetika en inplantbare toestelle vereis presisiebewerking vir bioversoenbaarheid, akkuraatheid en pasiëntveiligheid.
- Motorsektor: Presisie-bewerkte onderdele is noodsaaklik vir die motorbedryf om die betroubaarheid en doeltreffendheid van voertuie te verseker. Komponente soos enjinonderdele, transmissiestelsels en remmeganismes maak staat op presiese bewerking.
- Elektronika en halfgeleiers: Presisiebewerking is deurslaggewend in die vervaardiging van mikro-elektroniese komponente en halfgeleiertoestelle, waar minuskulêre toleransies noodsaaklik is vir funksionaliteit.
- Energiesektor: Die energiebedryf maak staat op presisiebewerking vir die vervaardiging van kritieke onderdele wat in kragopwekking gebruik word, insluitend turbines, kragopwekkers en transmissiekomponente.
- Gereedskap en Matrijs maak: Presisiebewerking is deurslaggewend in die vervaardiging van gereedskap en matryse, wat op hul beurt gebruik word om talle ander produkte te skep.
- Consumer Electronics: Die vervaardiging van slimfone, skootrekenaars en ander verbruikerselektronika trek voordeel uit presisiebewerking om slanke ontwerpe en optimale funksionaliteit te verseker.
- Navorsing en ontwikkeling: Navorsers en wetenskaplikes is afhanklik van presisie-gemasjineerde komponente vir eksperimente, prototipes en laboratoriumtoerusting.
C. Historiese Perspektief
Die reis van presisiebewerking gaan terug na antieke beskawings, waar bekwame ambagsmanne rudimentêre gereedskap gebruik het om materiale te vorm. Die akkuraatheid wat in daardie tye behaal is, was egter beperk in vergelyking met kontemporêre standaarde.- Vroeë presisiebewerking: Die industriële rewolusie van die 18de en 19de eeue was 'n deurslaggewende tydperk in die ontwikkeling van presisiebewerking. Die uitvinding van masjiengereedskap, soos draaibanke en freesmasjiene, het vervaardiging 'n rewolusie teweeggebring deur groter akkuraatheid en konsekwentheid moontlik te maak.
- Tweede Wêreldoorlog: Presisiemasjinering het 'n deurslaggewende rol in die Tweede Wêreldoorlog gespeel, aangesien dit noodsaaklik was vir die vervaardiging van militêre toerusting met die vereiste akkuraatheid en eenvormigheid. Hierdie era was getuie van vooruitgang in bewerkingstegnieke en die opkoms van nuwe materiale.
- Na-oorlogse vooruitgang: Die na-oorlogse tydperk het 'n oplewing in tegnologiese innovasies, insluitend die gebruik van rekenaar numeriese beheer (CNC) masjiene. CNC bewerking geoutomatiseerde en hoogs presiese bewerkings moontlik gemaak, wat 'n nuwe era van vervaardiging inlui.
- Die Digitale Era: Die integrasie van rekenaars en sagteware in bewerkingsprosesse het presisiebewerking verder verhoog. Moderne CNC-masjiene kan komplekse bewerkings met ongeëwenaarde akkuraatheid uitvoer, wat hulle onontbeerlik maak in vandag se vervaardigingslandskap.
Materiaal en hul betekenis
Materiale is die grondslag van presisiebewerking, en die keuse van die regte materiaal speel 'n deurslaggewende rol in die vervaardiging van hoë-presisie-onderdele. In hierdie afdeling sal ons delf na die belangrikheid van die keuse van die gepaste materiale, die belangrikheid van materiaaleienskappe verstaan en die verskillende faktore wat bewerkbaarheid beïnvloed, ondersoek.A. Seleksie van materiale
Die keuse van materiale in presisiebewerking is 'n kritieke besluit wat die werkverrigting, duursaamheid en funksionaliteit van die finale produk direk beïnvloed. Vervaardigers moet verskeie faktore oorweeg wanneer hulle materiaal kies:- Materiaal geskiktheid: Die materiaal moet geskik wees vir die beoogde toepassing. Verskillende nywerhede en toepassings het verskillende vereistes, soos temperatuurweerstand, korrosieweerstand en elektriese geleidingsvermoë.
- Meganiese eienskappe: Meganiese eienskappe soos treksterkte, hardheid en rekbaarheid is deurslaggewend. Byvoorbeeld, in die ruimtevaart word materiale met hoë treksterkte verkies vir strukturele komponente.
- Termiese eienskappe: Sommige toepassings vereis materiale met uitstekende termiese geleidingsvermoë of weerstand teen hoë temperature. Dit is veral belangrik in nywerhede soos kragopwekking en elektronika.
- Weerstand teen korrosie: In omgewings waar korrosie 'n bekommernis is, word materiale met hoë weerstand teen korrosie, soos vlekvrye staal of titanium, verkies.
- Gewig oorwegings: Nywerhede soos motor- en lugvaart prioritiseer dikwels liggewigmateriale soos aluminium- of koolstofveselsamestellings om brandstofverbruik te verminder en werkverrigting te verbeter.
- Kostebeperkings: Koste is 'n beduidende faktor in materiaalkeuse. Hoë-werkverrigting materiale kan duur wees, so vervaardigers moet 'n balans tussen werkverrigting en koste-effektiwiteit vind.
- Wetlike voldoening: In nywerhede soos gesondheidsorg moet materiaal voldoen aan streng regulatoriese standaarde vir bioversoenbaarheid en veiligheid.
- Beskikbaarheid : Die beskikbaarheid van materiale en hul bronne beïnvloed ook seleksie. Sommige gespesialiseerde legerings of komposiete kan beperkte beskikbaarheid hê.
B. Materiële eienskappe
Om die eienskappe van materiale te verstaan is noodsaaklik vir presisiebewerking. Hier is 'n paar belangrike materiaal eienskappe en hul betekenis:- Treksterkte: Treksterkte meet 'n materiaal se vermoë om 'n trekkrag te weerstaan sonder om te breek. Dit is noodsaaklik vir strukturele komponente en dele wat aan meganiese spanning onderwerp word.
- Hardheid: Hardheid dui op 'n materiaal se weerstand teen vervorming en slytasie. Harde materiale is geskik vir snygereedskap, terwyl sagter materiale verkies kan word vir sekere toepassings, soos seëls.
- smeebaarheid: Duktiliteit verwys na 'n materiaal se vermoë om te vervorm sonder om te breek wanneer dit aan trekspanning onderwerp word. Vervormbare materiale is makliker om te vorm, maar is dalk nie geskik vir toepassings wat styfheid vereis nie.
- Termiese geleidingsvermoë: Materiale met hoë termiese geleidingsvermoë verdryf hitte doeltreffend. Hierdie eienskap is noodsaaklik in toepassings waar temperatuurbeheer krities is.
- Elektriese geleiding: Elektriese geleiding is noodsaaklik in elektronika en elektriese komponente, waar materiale die vloei van elektrisiteit moet vergemaklik.
- Magnetiese eienskappe: Magnetiese eienskappe is betekenisvol in nywerhede soos elektromagnetika en elektronika, waar materiale ferromagneties of nie-magneties mag wees.
- Chemiese Weerstand: Materiale moet chemiese korrosie weerstaan in omgewings waar hulle aan sure, basisse of ander korrosiewe stowwe blootgestel word.
C. Bewerkbaarheidsfaktore
Bewerkbaarheid verwys na die gemak waarmee 'n materiaal gemasjineer, gesny of gevorm kan word. Dit word beïnvloed deur verskeie faktore, insluitend:- Materiaal hardheid: Sagter materiale is oor die algemeen makliker om te masjineer, terwyl harder materiale gespesialiseerde gereedskap en tegnieke kan vereis.
- Chip vorming: Die vorming en ontruiming van skyfies tydens bewerking beïnvloed die proses se doeltreffendheid en oppervlakafwerking.
- Gereedskapdrag: Verskillende materiale kan verskillende grade van gereedskapslytasie veroorsaak, wat die bewerkingspoed en -koste beïnvloed.
- Koelmiddel en smeermiddel: Behoorlike koelmiddel en smering is noodsaaklik om wrywing, hitte en gereedskapslytasie tydens bewerking te verminder.
- Sny Spoed: Die spoed waarteen die snygereedskap deur die materiaal beweeg, beïnvloed beide produktiwiteit en die kwaliteit van die bewerkte oppervlak.
- Gereedskap Materiaal: Die keuse van snygereedskapmateriaal, soos karbied of hoëspoedstaal, hang af van die materiaal wat gemasjineer word.
- Sny parameters: Die aanpassing van snyparameters soos toevoertempo en snydiepte kan die bewerkingsproses vir spesifieke materiale optimaliseer.
Masjiengereedskap vir presisiebewerking
Masjiengereedskap is die hart van presisiebewerking, wat die transformasie van grondstowwe in hoë-presisie-onderdele moontlik maak. In hierdie afdeling sal ons vier sleuteltipes masjiengereedskap wat in presisiebewerking gebruik word, verken: CNC-bewerkingsentrums, Draaimasjiene, Slypmasjiene en EDM (Elektriese Ontladingsbewerking). Elkeen van hierdie masjiene speel 'n unieke rol in die vervaardiging van presiese komponente.A. CNC-bewerkingsentrums
CNC (Computer Numerical Control) bewerkingsentrums is veelsydig en word wyd gebruik in presisie bewerking. Dit is geoutomatiseerde stelsels wat die beweging van snygereedskap en werkstukke met uitsonderlike presisie beheer. Hier is 'n oorsig van CNC-bewerkingsentrums en hul betekenis:- veelsydigheid: CNC-bewerkingsentrums kan verskeie bewerkingsoperasies uitvoer, insluitend frees, boor en tap. Hierdie veelsydigheid maak voorsiening vir die vervaardiging van komplekse onderdele met veelvuldige kenmerke.
- 'n hoë presisie: Die gerekenariseerde beheer van CNC-masjiene verseker presiese gereedskapposisionering en konsekwente resultate, wat hulle ideaal maak vir onderdele met stywe toleransies.
- Automation: CNC-bewerkingsentrums kan deurlopend werk, met minimale menslike ingryping. Hierdie outomatisering verhoog doeltreffendheid en verminder die risiko van foute.
- Komplekse geometrieë: Hulle blink uit in die bewerking van ingewikkelde vorms en kontoere, wat hulle geskik maak vir nywerhede soos lugvaart, waar komplekse komponente algemeen voorkom.
- Herhaalbare resultate: CNC-masjiene bied uitstekende herhaalbaarheid, om te verseker dat elke onderdeel wat vervaardig word, ooreenstem met die presiese spesifikasies van die ontwerp.
- Verminderde opsteltye: CNC-bewerkingsentrums kan geprogrammeer word om vinnig tussen verskillende take te wissel, wat opsteltye tot die minimum beperk en produksiedoeltreffendheid verhoog.
B. Draaimasjiene
Draaimasjiene word gebruik om silindriese dele te skep deur 'n werkstuk te draai terwyl 'n snygereedskap materiaal van sy buitenste oppervlak verwyder. Hulle is noodsaaklik vir produksie skags, penne en ander komponente met rotasiesimmetrie. Sleutelpunte oor draaimasjiene sluit in:- Silindriese dele: Draaimasjiene spesialiseer in die vervaardiging van silindriese of buisvormige komponente, insluitend dié met drade of ingewikkelde groewe.
- Hoë snelhede: Hulle werk teen hoë snelhede, wat hulle geskik maak vir onderdele wat 'n gladde en akkurate afwerking vereis.
- Enkel-as werking: Die meeste draaimasjiene is enkel-as en fokus op die vorming van die eksterne oppervlak van die werkstuk.
- Doeltreffend vir massaproduksie: Draai is hoogs doeltreffend vir massavervaardiging van onderdele met minimale materiaalvermorsing.
- Draaibank masjiene: Handmatige en CNC-beheerde draaibankmasjiene is algemeen gebruikte draaimasjiene, wat 'n reeks vermoëns bied.
C. Slypmasjiene
Slypmasjiene is ontwerp vir presisie oppervlakafwerking en vorming van harde of skuur materiale. Hulle is van kardinale belang vir die bereiking van uiters stywe toleransies en uitstekende oppervlakafwerkings. Hier is hoekom slypmasjiene belangrik is:- Mikronvlak-presisie: Slypmasjiene kan mikronvlak-presisie bereik, wat dit noodsaaklik maak vir toepassings wat die hoogste vlak van akkuraatheid vereis.
- Materiaal verwydering: Hulle verwyder materiaal deur skuur, wat voorsiening maak vir die regstelling van oppervlak-onvolmaakthede en die bereiking van uitsonderlike gladheid.
- Gereedskap en snyer Slyp: Benewens oppervlakslyp, is daar gespesialiseerde slypmasjiene vir die slyp van snygereedskap en die vervaardiging van presiese profiele.
- Verskeidenheid slypmetodes: Verskillende soorte slypmasjiene, insluitend oppervlakslypers, silindriese slypmasjiene, en middellose slypmasjiene, voorsien in verskeie bewerkingsbehoeftes.
- Geharde materiale: Slyp is veral geskik vir geharde materiale soos gereedskapstaal en keramiek, waar tradisionele bewerkingsmetodes ondoeltreffend kan wees.
D. EDM (Elektriese Ontladingsbewerking)
EDM, of Electrical Discharge Machining, is 'n nie-tradisionele bewerkingsproses wat elektriese ontladings gebruik om materiale te vorm. Dit is ideaal vir die skep van ingewikkelde en delikate dele waar tradisionele snygereedskap skade kan veroorsaak. Sleutelaspekte van EDM sluit in:- Geen fisiese kontak nie: EDM behels nie direkte fisiese kontak tussen die werktuig en werkstuk nie, wat die risiko van gereedskapslytasie en skade aan brose materiale tot die minimum beperk.
- 'n hoë presisie: Dit kan hoë akkuraatheid en oppervlakafwerkingsgehalte behaal, selfs met buitengewone harde materiale.
- Draad-EDM en sinker-EDM: Daar is twee primêre tipes EDM-masjiene: draad sny EDM, wat 'n draadelektrode gebruik, en sinker EDM, wat 'n gevormde elektrode gebruik.
- Komplekse vorms: EDM kan komplekse vorms produseer, soos matryse en vorms, met ingewikkelde besonderhede en fyn kenmerke.
- Hitte-geaffekteerde sone: Aangesien EDM nie hitte by die werkstuk genereer nie, is dit geskik vir hitte-sensitiewe materiale soos lugvaartlegerings.
- Stadige proses: EDM is relatief stadig in vergelyking met ander bewerkingsmetodes, wat dit die beste geskik maak vir lae-hoeveelheid, hoë-presisie take.
Snygereedskap en gereedskap
Snygereedskap is aan die voorpunt van presisiebewerking, en dien as die instrumente wat grondstowwe vorm en omskep in hoë-presisie-onderdele. In hierdie afdeling sal ons die verskillende soorte snygereedskap ondersoek, die belangrikheid van gereedskapbedekkings en die faktore wat gereedskapleeftyd en slytasie beïnvloed.A. Tipes snygereedskap
Presisiebewerking maak staat op 'n diverse reeks snygereedskap, elk ontwerp vir spesifieke take en materiale. Die keuse van snygereedskap beïnvloed die doeltreffendheid en akkuraatheid van die bewerkingsproses grootliks. Hier is 'n paar algemene tipes snygereedskap:- End Mills: Eindmeulens is veelsydige gereedskap wat vir maalbewerkings gebruik word. Hulle het veelvuldige snykante en kan materiaal op verskeie maniere van die werkstuk verwyder, insluitend gesig, kontoer en gleuf.
- Drills: Bore is ontwerp om gate in werkstukke te skep. Hulle kom in verskeie vorme voor, insluitend draaibore, middelbore en indekseerbare bore.
- Draai-insetsels: Dit word in draaimasjiene gebruik om silindriese dele te vorm. Draai-insetsels is beskikbaar in 'n verskeidenheid vorms en materiale om by verskillende toepassings te pas.
- Meulsnyers: Freessnyers kom in verskillende vorms voor, soos vlakmeulens, balmeulens en gleufsnyers, en word in freesmasjiene gebruik om verskeie kenmerke op die werkstuk te skep.
- ruimers: Ruimers word gebruik vir die afwerking en grootte van voorheen geboorde gate tot presiese afmetings. Hulle verseker gladde en akkurate gatoppervlaktes.
- Taps and Dies: Hierdie snygereedskap word gebruik vir inrygbewerkings. Krane skep interne drade, terwyl matryse eksterne drade skep.
- Slypwiele: Slypwiele is skuurgereedskap wat gebruik word vir presisie oppervlak slyp. Hulle is beskikbaar in verskeie skuurmateriaal en korrelgroottes.
- struikel: Broches is gespesialiseerde gereedskap wat gebruik word vir die sny van interne en eksterne vorms en profiele, soos spiebane en splines.
- Teenborings en Countersinks: Hierdie gereedskap word gebruik om uitsparings of afkante rondom gate vir te skep sluitings.
- Vervelige bars: Boorstawe word in boorbewerkings gebruik om bestaande gate met presisie te vergroot.
B. Gereedskapbedekkings
Gereedskapbedekkings is dun lae materiaal wat op snygereedskap toegepas word om hul werkverrigting en duursaamheid te verbeter. Hierdie bedekkings bied verskeie voordele:- Verminderde wrywing: Bedekkings soos titaniumnitried (TiN) en titaniumkarbonitried (TiCN) verminder wrywing tussen die werktuig en werkstuk, wat lei tot gladder snywerk en langer werktuiglewe.
- Verbeterde hardheid: Bedekkings verhoog die hardheid van die werktuig se oppervlak, maak dit meer bestand teen slytasie en verleng die werktuiglewe.
- Verbeterde hitteweerstand: Bedekkings kan hoë temperature weerstaan wat tydens bewerking gegenereer word, wat hitteverwante gereedskapslytasie verminder en snyspoed verhoog.
- Anti-opbou-eienskappe: Sommige bedekkings het anti-adhesie eienskappe, wat die opbou van materiaal op die gereedskap se snykante voorkom.
- Verhoogde smering: Bedekte gereedskap het verbeterde smering, wat die behoefte aan oormatige koelmiddel verminder en die spaan-ontruiming verbeter.
C. Gereedskapslewe en -slytasie
Om die lewensduur en slytasie van gereedskap te verstaan, is noodsaaklik vir die optimalisering van bewerkingsprosesse en die vermindering van produksiekoste. Gereedskapslewe verwys na die tydsduur wat 'n snywerktuig doeltreffend bly voordat dit vervanging of herkondisionering benodig. Verskeie faktore beïnvloed gereedskapleeftyd en slytasie:- Sny Spoed: Hoër snyspoed kan lei tot verhoogde gereedskapslytasie as gevolg van hoër temperature wat tydens bewerking gegenereer word. Behoorlike keuse van snyspoed is noodsaaklik om werktuiglewe en produktiwiteit te balanseer.
- Voer koers: Die tempo waarteen die snygereedskap in die werkstuk beweeg, beïnvloed gereedskapslytasie. Hoë voertempo's kan slytasie versnel, terwyl laer voertempo's gereedskaplewe kan verleng.
- Diepte van die sny: Die snydiepte beïnvloed die hoeveelheid materiaal wat per pas verwyder word. Dieper snitte kan gereedskapslytasie verhoog, dus die optimalisering van diepte is van kritieke belang.
- Materiaal hardheid: Die sny van harde materiale kan slytasie van gereedskap versnel. Gespesialiseerde gereedskap en bedekkings word gebruik vir die doeltreffende bewerking van harde materiale.
- Koelmiddel en smeermiddel: Behoorlike koelmiddel en smering help om hitte te verdryf en wrywing te verminder, wat die werktuiglewe verleng.
- Gereedskap Materiaal: Die materiaal waaruit die snywerktuig gemaak is, beïnvloed sy slytasieweerstand. Materiale soos karbied en keramiek bied uitstekende slytasieweerstand.
- Gereedskap meetkunde: Die geometrie van die snygereedskap, insluitende harkhoek, reliëfhoek en spaanderbreker-ontwerp, speel 'n beduidende rol in slytasiepatrone.
- Werkstuk Materiaal: Die tipe materiaal wat gemasjineer word, beïnvloed gereedskapslytasie. Skuurmateriaal kan lei tot vinniger slytasie van gereedskap.
Presisiebewerkingsprosesse
Presisiebewerkingsprosesse is die metodes waardeur grondstowwe omskep word in hoë-presisie-onderdele met streng toleransies en uitsonderlike oppervlakafwerkings. In hierdie afdeling sal ons vyf sleutel-presisiebewerkingsprosesse ondersoek: draai, frees, boor, slyp en elektriese ontladingsbewerking (EDM). Elkeen van hierdie prosesse dien 'n unieke doel en word aangewend op grond van die spesifieke vereistes van die werkstuk.A. Draai
Draai is 'n bewerkingsproses wat hoofsaaklik gebruik word vir die vorming van silindriese dele. Dit behels die rotasie van 'n werkstuk terwyl 'n enkelpuntsnywerktuig materiaal van die buitenste oppervlak verwyder. Hier is die sleutelaspekte van draai:- Silindriese dele: Draai is ideaal vir die vervaardiging van silindriese komponente soos skagte, penne en hulse.
- Rotasie-simmetrie: Dit is goed geskik vir dele wat rotasiesimmetrie vereis, aangesien die werkstuk op 'n draaibank roteer terwyl die snygereedskap dit vorm.
- Verskeie operasies: Draai kan verskeie bewerkings uitvoer, insluitend nadraai, draai (verminder die deursnee), tapse draai en skroefdraad.
- Enkelpuntsny: 'n Enkele snywerktuig verwyder materiaal in 'n deurlopende beweging, wat lei tot doeltreffende materiaalverwydering.
- Draaibank masjiene: Beide hand- en CNC-beheerde draaibankmasjiene word algemeen gebruik vir draaibewerkings.
B. Meulwerk
Freeswerk is 'n veelsydige presisiebewerkingsproses wat meerpuntsnygereedskap gebruik om materiaal van 'n werkstuk te verwyder. Dit is goed geskik om 'n wye verskeidenheid vorms en kenmerke te skep. Sleutelaspekte van maalwerk sluit in:- veelsydigheid: Freeswerk kan plat oppervlaktes, gleuwe, sakke en komplekse kontoere produseer. Dit word gebruik vir beide 2D- en 3D-bewerking.
- Multi-punt sny: Veelvuldige snykante op die werktuig werk gelyktydig in wisselwerking met die werkstuk, wat doeltreffende materiaalverwydering moontlik maak.
- Tipes maalwerk: Freule kan uitgevoer word met behulp van verskeie soorte snyers, insluitend eindmeulens, vlakmeulens en balmeulens.
- CNC-bewerkingsentrums: CNC-beheerde freesmasjiene bied presiese beheer oor werktuigbeweging en word wyd in moderne bewerking gebruik.
- Hoë snelhede: Meulwerk kan teen hoë snelhede uitgevoer word, wat doeltreffende produksie moontlik maak.
C. Boorwerk
Boor is 'n presisie bewerkingsproses wat gebruik word om gate in werkstukke te skep. Dit is 'n fundamentele operasie in verskeie industrieë. Sleutel aspekte van boor sluit in:- Gatskepping: Boormasjiene gebruik gespesialiseerde gereedskap genaamd bore om materiaal te verwyder en gate van spesifieke deursnee te skep.
- Tipes bore: Verskillende tipes bore is beskikbaar, insluitend draaibore, middelbore en indekseerbare bore, elk ontwerp vir spesifieke toepassings.
- Akkuraatheid: Presiese posisionering en belyning is noodsaaklik by boor om te verseker dat gate met akkuraatheid geskep word.
- Spoed en Voertempo: Boorparameters soos rotasiespoed en toevoertempo is krities vir die bereiking van verlangde gatafmetings.
- Koelmiddel en smeermiddel: Behoorlike koelmiddel en smeermiddel word gebruik om hitte te verdryf en wrywing tydens boor te verminder.
D. Maalwerk
Slyp is 'n presisie bewerkingsproses wat skuurwiele gebruik om materiaal te verwyder en uiters streng toleransies en oppervlakafwerkings te bereik. Sleutel aspekte van slyp sluit in:- Uitsonderlike presisie: Slyp kan mikronvlak-presisie bereik, wat dit ideaal maak vir toepassings wat die hoogste akkuraatheid vereis.
- oppervlak: Dit lewer voortreflike oppervlakafwerkings, wat dikwels die behoefte aan bykomende afwerkingsprosesse uitskakel.
- Materiale: Slyp is geskik vir harde en skuur materiale, insluitend geharde staal, keramiek en karbiede.
- Verskeidenheid slypmetodes: Verskillende soorte slypmasjiene, soos oppervlakslypers, silindriese slypmasjiene, en middellose slypmasjiene, voorsien in verskeie bewerkingsbehoeftes.
- Koelvloeistof: Behoorlike koelmiddel is noodsaaklik in slyp om oorverhitting te voorkom en wielintegriteit te behou.
E. Elektriese ontladingsbewerking (EDM)
EDM, of Electrical Discharge Machining, is 'n nie-tradisionele presisie bewerkingsproses wat elektriese ontladings gebruik om materiaal te verwyder. Dit is veral geskik vir die bewerking van komplekse en ingewikkelde vorms, sowel as harde en hittebestande materiale. Sleutelaspekte van EDM sluit in:- Nie-kontak bewerking: EDM behels nie direkte kontak tussen die gereedskap en werkstuk nie, wat die risiko van gereedskapslytasie en skade verminder.
- 'n hoë presisie: EDM kan hoë presisie bereik, wat dit geskik maak vir toepassings waar streng toleransies noodsaaklik is.
- Komplekse vorms: Dit blink uit in die bewerking van komplekse vorms, matryse, vorms en komponente met fyn besonderhede.
- Draad-EDM en sinker-EDM: Daar is twee primêre tipes EDM-masjiene: draad-EDM, wat 'n draadelektrode gebruik, en sinker-EDM, wat 'n gevormde elektrode gebruik.
- Stadige proses: EDM is relatief stadig in vergelyking met ander bewerkingsmetodes, wat dit die beste geskik maak vir lae-hoeveelheid, hoë-presisie take.
Toleransies en kwaliteitbeheer
Presisie bewerking vereis noukeurige aandag aan detail en 'n streng verbintenis tot gehaltebeheer om te verseker dat onderdele aan die gespesifiseerde standaarde voldoen. In hierdie afdeling sal ons drie kritieke aspekte van gehaltebeheer in presisiebewerking ondersoek: Geometriese Dimensionering en Toleransie (GD&T), Statistiese Prosesbeheer (SPC) en Gehalteversekering.A. Geometriese afmetings en toleransie (GD&T)
Geometriese Dimensionering en Toleransie, dikwels afgekort as GD&T, is 'n stelsel wat gebruik word om die toelaatbare variasies in grootte, vorm, oriëntasie en ligging van kenmerke op 'n onderdeel te definieer en te kommunikeer. GD&T is noodsaaklik in presisiebewerking om die volgende redes:- Presiese kommunikasie: GD&T bied 'n gestandaardiseerde taal vir ingenieurs, ontwerpers en masjiniste om ontwerpbedoeling en dimensionele vereistes akkuraat te kommunikeer.
- Verdraagsaamheid Verklaring: Dit help om die aanvaarbare variasie in kritieke dimensies te definieer, om te verseker dat alle belanghebbendes die toelaatbare afwykings verstaan.
- Verbeterde kwaliteit: GD&T bevorder verbeterde kwaliteit deur dubbelsinnigheid in ontwerpspesifikasies te verminder, wat die risiko van foute tydens bewerking tot die minimum beperk.
- Koste-effektiwiteit: Duidelike GD&T-spesifikasies kan lei tot verlaagde vervaardigingskoste, aangesien onderdele minder geneig is om geskrap te word of herbewerking vereis as gevolg van misverstand of verkeerde interpretasie.
- Komplekse meetkunde: Dit is veral nuttig vir onderdele met komplekse geometrieë, om te verseker dat alle kenmerke volgens die verlangde spesifikasies vervaardig word.
B. Statistiese Prosesbeheer (DBK)
Statistiese Prosesbeheer (SPC) is 'n gehaltebeheermetodologie wat statistiese tegnieke gebruik om die bewerkingsproses te monitor en te beheer. SPC is noodsaaklik in presisiebewerking om die volgende redes:- Prosesmonitering: SPC help om bewerkingsprosesse intyds te monitor, en identifiseer variasies of afwykings van die verlangde parameters.
- Vroeë opsporing van kwessies: Deur die proses deurlopend te monitor, maak SPC voorsiening vir die vroeë opsporing van probleme wat kan lei tot buite-spesifikasie onderdele, wat vermorsing en herbewerking verminder.
- Datagedrewe besluitneming: SPC maak staat op data en statistiese analise om ingeligte besluite oor prosesaanpassings te neem, om te verseker dat die bewerkingsproses binne aanvaarbare perke bly.
- Verbeterde konsekwentheid: SPC bevorder proseskonsekwentheid en verminder die waarskynlikheid dat nie-konformerende dele vervaardig word.
- Verminder skroot en herbewerking: Deur prosesvariasies stiptelik te identifiseer en aan te spreek, verminder SPC die produksie van defekte onderdele, wat skroot- en herbewerkingskoste verminder.
C. Gehalteversekering in presisiebewerking
Gehalteversekering in presisiebewerking sluit 'n omvattende benadering in om te verseker dat vervaardigde onderdele aan gespesifiseerde kwaliteitstandaarde voldoen of oorskry. Dit behels verskeie elemente, insluitend:- Proses dokumentasie: Gedetailleerde dokumentasie van bewerkingsprosesse, insluitend standaard bedryfsprosedures (SOP's) en werkinstruksies, verseker dat elke stap konsekwent uitgevoer word.
- Inspeksie en meting: Streng inspeksie en meting deur gebruik te maak van presisie-instrumente en metrologietegnieke verifieer dat onderdele voldoen aan gespesifiseerde toleransies en kwaliteitstandaarde.
- Kalibrasie: Gereelde kalibrasie van bewerkingstoerusting en meetinstrumente is noodsaaklik om akkuraatheid en naspeurbaarheid te handhaaf.
- Materiaalverifikasie: Verifikasie van materiaal eienskappe, samestelling en kwaliteit is van kritieke belang om te verseker dat die materiaal wat gebruik word voldoen aan ontwerp vereistes.
- Werknemeropleiding: Opleidings- en vaardigheidsontwikkelingsprogramme vir masjiniste en kwaliteitbeheerpersoneel verseker dat hulle vaardig is in hul rolle en verantwoordelikhede.
- Oorsprongsanaliese: Wanneer nie-konformerende dele geïdentifiseer word, word grondoorsaak-analise uitgevoer om die bron van die probleem te bepaal en regstellende aksies te implementeer.
- Deurlopende verbetering: 'n Kultuur van voortdurende verbetering bevorder innovasie en dryf voortdurende verbeterings in bewerkingsprosesse en kwaliteitbeheerprosedures aan.
- Customer Feedback: Die versameling en ontleding van kliënteterugvoer help om gebiede vir verbetering te identifiseer en belyn bewerkingsprosesse met kliënte se verwagtinge.
Gevolgtrekking
A. Die kuns en wetenskap van presisiebewerking
Presisiebewerking staan op die kruising van kuns en wetenskap, waar kreatiwiteit, vaardigheid en innovasie saamvloei om hoë-presisie-onderdele te produseer wat nywerhede aandryf en die moderne wêreld vorm. Dit is beide 'n kunsvorm wat die vakmanskap en kundigheid vereis van masjiniste wat grondstowwe in werke van ingenieursuitnemendheid omskep, en 'n wetenskap wat staatmaak op die nuutste tegnologie, materiaalwetenskap en gevorderde prosesse om ongeëwenaarde akkuraatheid te bereik. Die reis van presisiebewerking neem ons deur die begrip van materiale en hul eienskappe, die bemeestering van snygereedskap en masjinerie, en die noukeurige beheer van prosesse en toleransies. Dit sluit die taal van meetkundige dimensionering en verdraagsaamheid in, die waaksaamheid van statistiese prosesbeheer, en die verbintenis tot gehalteversekering. Presisiebewerking speel 'n deurslaggewende rol in diverse industrieë, van lugvaart en motor tot mediese toestelle en elektronika, en vorm alles van vliegtuigenjins tot kunsmatige gewrigte en mikroskyfies. Dit maak die skepping van komponente moontlik wat met ongeëwenaarde akkuraatheid en betroubaarheid werk, wat dikwels die grense verskuif van wat moontlik is.B. Finale Gedagtes
Soos ons hierdie verkenning van presisiebewerking afsluit, is dit duidelik dat hierdie veld nie net oor die skepping van onderdele gaan nie; dit gaan oor die skepping van moontlikhede. Die strewe na presisie dryf innovasie aan en verskuif die grense van wat bereik kan word. Of dit nou die delikate vakmanskap is wat nodig is om 'n horlosie se ingewikkelde ratte te skep of die gevorderde tegnologie wat nodig is om komplekse lugvaartkomponente te vervaardig, presisiebewerking is die kern van alles. Die toekoms van presisiebewerking is vol belofte. Vooruitgang in materiaalwetenskap, outomatisering en digitale tegnologieë gaan voort om die landskap te hervorm. Miniaturisering, 3D-drukwerk en volhoubare vervaardigingspraktyke word toenemend prominent, wat nuwe horisonne vir die bedryf inlui. In 'n wêreld waar presisie meer saak maak as ooit, bly presisiebewerking 'n onontbeerlike pilaar van moderne ingenieurswese. Dit is 'n bewys van menslike vernuf en ons onwrikbare strewe na uitnemendheid in elke faset van vervaardiging. Namate die vraag na hoër akkuraatheid en meer ingewikkelde komponente toeneem, sal presisiebewerking voortgaan om te ontwikkel en die uitdagings van môre met dieselfde toewyding en presiesheid tegemoet te gaan wat dit al eeue lank gedefinieer het.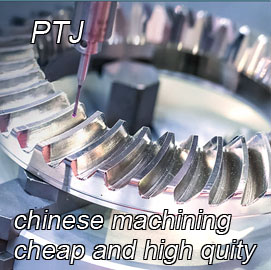
ons Dienste
- 5 Asbewerking
- Cnc frees
- CNN draai
- Bewerkingsbedrywe
- Bewerkingsproses
- Oppervlak behandeling
- Metaalbewerking
- Plastiekbewerking
- Poeier Metallurgie Mould
- Die Casting
- Onderdelegalery
Gevallestudies
- Auto Metal Onderdele
- Masjinerie Onderdele
- LED koelkop
- Gebouonderdele
- Mobiele onderdele
- Mediese onderdele
- Elektroniese onderdele
- Pasgemaakte bewerking
- fiets dele
Materiële lys
- Aluminiumbewerking
- Titaanbewerking
- Roesvrye staalbewerking
- Koperbewerking
- Koperbewerking
- Superlegeringsbewerking
- Loer bewerking
- UHMW -bewerking
- Eenvormige bewerking
- PA6 Bewerking
- PPS -bewerking
- Teflonbewerking
- Inconel -bewerking
- Gereedskapstaalbewerking
- Meer Materiaal
Onderdelegalery